Thoroughly remove the surface ash, oil, mold release agent, hollow drum and other materials that affect the construction of the wall surface. The surface protrusion of the wall should be removed when it is 10mm. For the clay brick wall, it is only necessary to remove the surface floating ash, white ash, etc., and the watering can be wetted. For the concrete wall and the masonry filled aerated concrete wall, the interface mortar should be sprayed.
As a representative of inorganic thermal insulation mortar, vitrified micro-bead insulation mortar has the advantages of high strength, light weight, thermal insulation, high bonding strength, fire resistance and weather resistance. It can be used as a fire barrier for external wall insulation system. The following is a brief analysis of the construction steps of the vitrified microbead insulation mortar fire barrier:
1, the basic wall treatment
Thoroughly remove the surface ash, oil, mold release agent, hollow drum and other materials that affect the construction of the wall surface of the base wall. When the surface protrusion of the wall is ≥10mm, it should be removed. For the clay brick wall, it is only necessary to remove the surface floating ash, white ash, etc., and the watering can be wetted. For the concrete wall and the masonry filled aerated concrete wall, the interface mortar should be sprayed.
2, insulation layer construction preparation
Hang vertical, set the square to find the rules, elastic thickness control line, pull vertical, horizontal control line. According to the thickness of the insulation layer required by the design, use the vitrified micro-bead insulation mortar to make the standard thickness gray cake and smash the rib to control the thickness of the insulation layer.
3, insulation layer construction
When the 300mm fireproof insulation tape is reserved, the extruded board of 50mm width and 300mm height may be used to adhere the mortar to the extruded board supporting the upper part of the fireproof insulation belt. The installation of the glass-coated micro-bead insulation mortar insulation layer is divided into at least 2-3 times. The insulation mortar for each application is 10-20mm. The thickness of the first construction should be controlled at about 10mm. Pay attention to compaction. The final construction thickness should be controlled at 10mm. Left and right, the construction interval should be more than 24h every two times. When the construction temperature is low, the interval can be extended. The vitrified microbead insulation mortar should be constructed from top to bottom. The last time the construction of the vitrified micro-bead insulation mortar insulation layer should reach the thickness of the gray cake blasting, and use the large bar to flatten the wall surface and the door window to meet the requirements. Pay attention to the compaction and compaction of the thermal insulation slurry. The prepared thermal insulation mortar should be used up within 4 hours. The thermal insulation mortar scraped off by the large bar must be re-used after being stirred within 4 hours. It is strictly forbidden to use the outdated thermal insulation mortar.
After the insulation layer is solidified and dried (by hand pressing the surface, about 2-3d), the next process can be carried out. If the ambient temperature is low, the curing time should be extended.
4, crack resistance layer construction
The fireproof isolation belt is coated with anti-cracking mortar to strengthen the alkali-resistant mesh cloth and the height of the mesh cloth is increased by 200mm. Use a trowel to first apply a 2-3mm crack-resistant mortar to the inorganic thermal insulation slurry and its upper and lower 200mm, and immediately press the mortar mesh into the crack-resistant mortar. The horizontal overlap of the mesh cloth adopts the dry lap joint method. Because the fireproof isolation belt is to be strengthened, in order to avoid excessive flatness error of the whole external wall insulation system, the vitrified microbead insulation mortar can be fired away from the upper and lower 200mm insulation board with an iron brush to reduce the thickness of 2-3mm. After the fireproof isolation belt and the large-surface insulation board are pasted and nailed into the anchor, the whole crack-resistant layer construction can be carried out according to the whole external wall insulation crack-resistant layer construction method.
Product navigation: fireproof material resin recycling glass wool
Foam glass insulation materials
Http://news.chinawj.com.cn
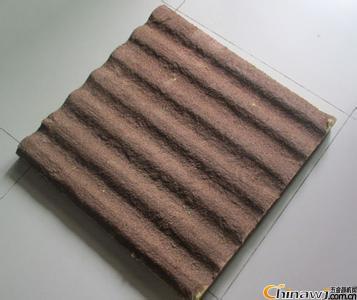
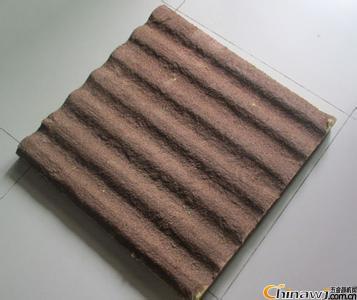
Granular Activated Carbon is the extension and supplement on products manufacturing and service of pellet series.
Granular activated carbon with different size distribution from US mesh4X8, 10X20, 20X40, 8X30, 6X12MESH, 8X16, 12X40 etc., also with different specifications including Iodine number, CTC, Ash, Moisture, PH value and so on;
Coal Granular Activated Carbon
Coal Granular Activated Carbon,Coal Based Granularcarbon,8X16 Mesh Coal Based Granular Carbon
Ningxia Huahui Activated Carbon Company Limited , https://www.huahurcarbon-tr.com