As the most typical aerospace structural components, the realization of efficient machining has always been a concern. The Shanghai Aerospace Precision Machinery Research Institute (hereinafter referred to as the “800â€) applied a solution from Seco Tools to improve the processing efficiency of a typical folding wing in an efficient process. And the surface quality is effectively guaranteed.
With the continuous development of science and technology, the rapid changes in the international situation, and the multi-party demand for new field exploration and homeland security, China's aerospace products have gradually entered a period of high-density launch, and the demand for various aerospace products is increasing year by year, forcing aerospace. Manufacturing companies must significantly increase their production capacity. The most important way is to improve processing efficiency.
At present, the most commonly used aerospace components are high-strength aluminum alloy materials (such as 2A12), which are easy-to-cut plastic materials with low strength and hardness, low melting point, good thermal conductivity and low tensile strength. However, the structural parts of aerospace products often have higher requirements on the machining accuracy, quality and processing efficiency of parts due to the complex shape structure, large material removal and thin wall deformation.
For example, a typical aerospace polyhedral part of a space consists of a plurality of angled bevels, and the overall wall thickness is thin and gradual. The blanks of such parts are generally pre-stretched aluminum plates, the thinnest part after processing is only 2mm, and the material removal rate of parts is more than 50%. In the machining process arrangement, the method of symmetric milling of the front and back of the thickness direction is most often used to uniformly remove the internal stress of the material release material to control the deformation of the part. It is precisely because the structure of the part is relatively complicated, and there are many rounded corners and inclined surfaces, which leads to complicated machining process, complicated tool path and low processing efficiency.
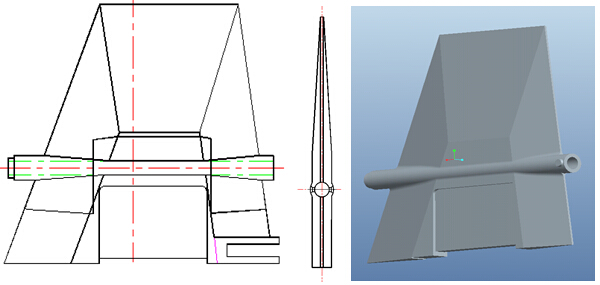
Fig.1 Two-dimensional schematic and three-dimensional model of aerospace typical thin polyhedral parts
Efficient machining requires system optimization
Efficient machining technology is characterized by high material removal rate and shorter single-piece machining time during machining, and is optimized by cutting parameters to ensure machining accuracy and surface quality. Compared to ordinary machining, it has a higher overall processing system. Claim. In the process of CNC milling of aerospace structural components, to ensure the machining quality and machining accuracy of the parts and to improve the material removal rate of the machining process, it must first be composed of the machine tool-tool-workpiece and their mutual interface (tool holder and fixture). The machining system is optimized to ensure the stability and reliability of the entire system during high-speed cutting.
The main purpose of roughing is to remove the material and leave a suitable margin for finishing. Therefore, roughing generally does not need to consider the dimensional accuracy of the workpiece, surface quality problems and deformation. In the finishing process, it is necessary to fully consider the influence of clamping, cutting and process parameters on the internal stress of the part, the influence of cutting force and cutting heat on the part structure during cutting, control the deformation, and avoid the accuracy of the parts caused by the deformation caused by the efficiency increase. Surface quality is destroyed.
Cutting tool selection
Choosing a more reasonable tool can directly increase production efficiency. The cutting process of aluminum alloy material is not very demanding on the tool material. Generally, the carbide milling cutter can be used, and the coating can be coated with no coating or diamond. In the roughing process, since it is not necessary to consider the accuracy and quality problems, and the metal material can be cut off to the maximum extent, the large-diameter tool can be selected to reduce the number of passes and shorten the pass time. In addition, in the roughing, try to choose a dense tooth cutter instead of the sparse cutter, which can increase the feed per revolution, and the cutting speed can be increased at the same speed. In the finishing process, in addition to considering the problem of efficient material removal, the problem of force deformation control during thin wall construction should be fully considered. For the finishing of aerospace aluminum alloy thin-walled parts, K-series carbide tools should be used (equivalent to China's original tungsten-cobalt, the main component is WC+Co, codenamed YG). The rake angle of the tool should not be too small, otherwise the cutting deformation and friction force will be increased, and the rake face wear will be increased to reduce the tool life.
Optimize the path of the knife
A more effective method for speed-increasing efficiency is to optimize the path of the tool. In the high-speed cutting, the directionality of the tool path should be guaranteed, that is, the tool path should be as simple as possible, with fewer turning points, the path should be as smooth as possible, and the rapid steering should be reduced; Knife time, increase the proportion of cutting time in the whole workpiece as much as possible; try to use circuit cutting, reduce the cutting and cutting times of the tool without interrupting the cutting process and tool path, and obtain a stable, high-efficiency and high-precision cutting process.
In the high-speed machining of large-scale complex curved surfaces of aerospace structural parts, when the curvature of the surface changes greatly, the direction of the maximum curvature radius should be taken as the optimal direction of the cutting, as shown in Figure 2.1; the curvature of the surface changes slowly, and the radius of curvature is the direction of the path. The influence is weakened, and the direction of the longest average length of a single tool rail should be selected, as shown in Figure 2.2.
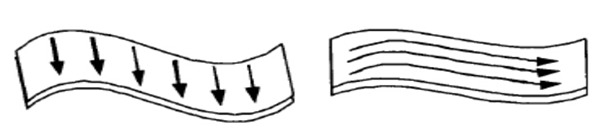
Figure 2.1: The path of the path with a small radius of curvature. Figure 2.2 The path of the path with a large radius of curvature.
In the case of beveling, if the horizontal horizontal pass shown in Figure 3.1 is used, the distance of each pass is very short. During the cutting process, the spindle needs frequent commutation and the cutting stability is poor. And because the cutting is a bevel, the horizontal pass requires the linkage of the X or Y axis and the Z axis, which is not conducive to the improvement of the cutting speed. Therefore, for such bevel machining, the path of the tool is arranged as parallel as possible to the longest bevel (see Figure 3.2). Not only is the path of the tool the longest, the number of commutations is the least, and the single path is only in the XY plane. The movement in the Z-axis direction is arranged outside the contour of the workpiece, and the tool damage can be reduced even under high-speed cutting.
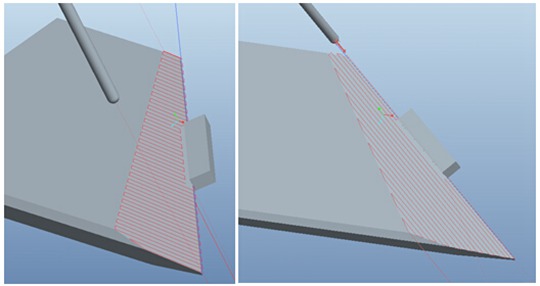
Figure 3.1 Horizontal horizontal path trajectory Figure 3.2 Orthogonal parallel path
Determination of cutting parameters
In roughing, "high-power" high-efficiency cutting with a large feed rate and a moderately large cutting depth combined with a medium cutting speed can be selected, and a high material removal rate can be achieved, thereby greatly improving production efficiency. For finishing, it is feasible to increase the rotational speed and increase the number of teeth. Increasing the feed per tooth may reduce the surface accuracy and cause residual stress to cause deformation. Therefore, the "light cut and fast cut" of the high cutting speed and low feed per tooth is often used to ensure the improvement of production efficiency and the accuracy and surface quality of the product.
Cutting parameters can be determined by cutting finite element analysis and cutting experiments. For example, through the finite element analysis at the processing site, the machine tool spindle with the highest speed of 24000r/min can be obtained to meet the high-speed machining process requirements of the typical aerospace aluminum alloy thin-walled structural parts. The spindle speed selection range is 15000r/min~ 20000r/min, while the feed per tooth and depth of cut should not be too large, the range of choice is 0.15 ~ 0.25mm / z and 3 ~ 5mm.
The cutting experiment was designed within the range of parameters obtained by finite element analysis. The cutting efficiency, surface roughness and surface topography were used as the criterion to determine the optimal cutting parameters.
Process improvement of typical folding wing
800 requires an efficient machining process improvement for a typical folding wing. The removal of each profile material of the wing parts accounts for 70% of the total material removal, and the time ratio in the processing is also very high. According to the above improvement ideas, by improving the tool and optimizing the cutting parameters, it is required to realize the lifting profile processing. Efficiency, while significantly reducing the manufacturing time of wing parts.
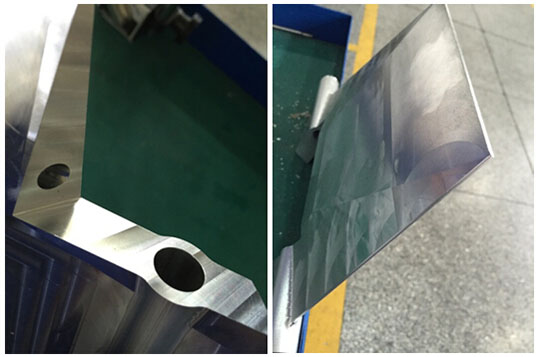
Figure 4 Part of the parts, the amount of material removal is very large
According to the multi-angle bevel, arc surface transition and high-precision hole groove characteristics of the part, DMG high-precision five-axis machining center is selected as the processing equipment. At the same time, the special hydraulic adjustable tooling is designed and manufactured, and a hydraulic power unit is used to provide power source for the special hydraulic tooling. The oil enters the hydraulic cylinder inside the tool body through the pipe to control the clamping and slack movement of the clamping original.
The improved R220.69-0050-10-5Aφ50 insert end mill with Seco Tools is equipped with XOEX10T304FR-E05, and the H15 insert finishes the roughing of each profile. The insert milling cutter has the characteristics of high rigidity and high economy compared with the original integrated cutter. The φ50 insert end mill selected this time is especially suitable for square shoulder milling. The length of the insert is 10mm, the maximum cutting Up to 9mm deep, a knife can simultaneously complete the processing of the end faces and sides of the wing parts. In order to improve the machining efficiency, the cutting is almost performed with full cutting width, the feed fz per tooth is about 0.05mm/tooth, and the feed speed is about 900m/min.
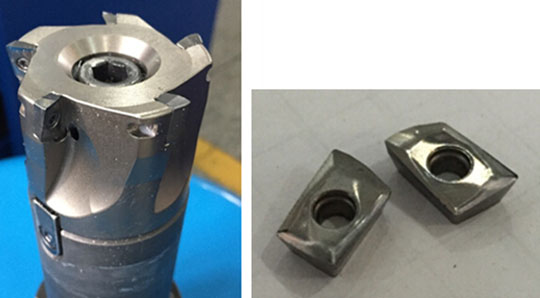
Figure 5 Seco Tools φ50 Insert Milling Cutter and Blade
In the finishing process of the wing part profile, since the side wall of the part is high, it is necessary to select a tool with a long overhang for cutting, so that the rigidity of the tool is put forward higher. 800 selected Seco Tools φ20 solid carbide end mill with heat shrink clamping shank to further improve cutting rigidity, as shown in Figure 6.
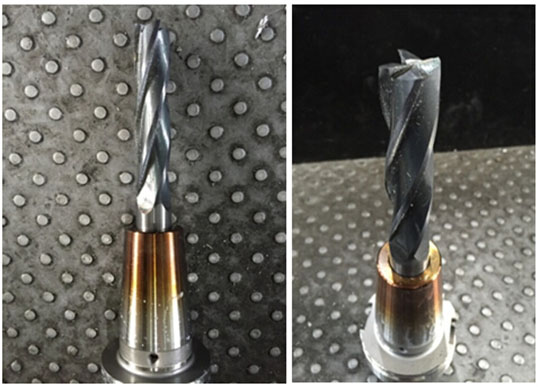
Figure 6 Seco tool φ20 solid carbide end mill clamped by heat shrinkable shank
After the high-efficiency improvement of the rough finishing of the wing part profile, the machining efficiency of the part is improved by more than 3 times, and the dimensional accuracy and surface quality of the part are effectively guaranteed. The surface profile of the profile processed before and after the improvement is shown in Fig. 7. In addition, in the high-speed cutting of finishing, the metal material is quickly cut off and separated from the surface of the workpiece, so that the burr around the part is significantly reduced, and the workload of the subsequent fitter is greatly reduced, further shortening the overall processing time of the part.
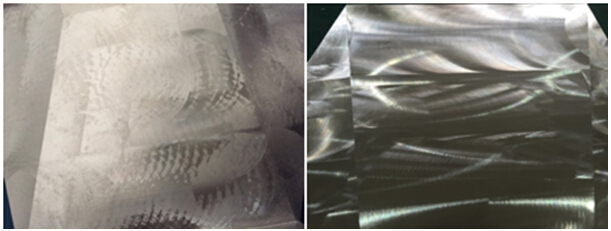
a) before improvement b) after improvement
Figure 7 Surface profile of the profile processed before and after improvement
Shanghai Aerospace Precision Machinery Research Institute
The 800th Research Institute of the 8th Research Institute of China Aerospace Science and Technology Corporation, also known as the Shanghai Aerospace Precision Machinery Research Institute, is the missile assembly unit of the Shanghai Aerospace Administration.
The 800th Research Institute is a research and manufacturing-oriented research institute with more than 30 majors. It has various advanced manufacturing and testing technologies, equipment and instruments. Models developed and approved for production include the Long March series of launch vehicles and spacecraft. It mainly undertakes the total assembly of air defense missiles, the processing of structural parts, the strength and environmental tests, and the production tasks of the rocket structure of the launch vehicle. It has strong professional and technical advantages in missile assembly comprehensive testing, strength and environmental testing, precision machining, magnesium alloy casting, aluminum alloy and stainless steel sheet welding, non-destructive testing and so on.
Seco knives
Headquartered in Fagersta, Sweden, Seco is committed to developing innovative metal cutting solutions and working closely with customers to fully understand and focus on meeting their needs. We employ more than 5,000 people in 50 countries and enhance the capabilities of our team members through training, development and employee recognition programs, and an open communication environment. Our employees demonstrate three core values ​​– hospitality, family belonging and personal commitment – ​​that define the way we do business and how we interact with our customers, suppliers and other partners. For more information, please visit
supervise, technology and advanced services. We have the advanced manufacturing equipment and quality test equipment for each batch of product testing. Also, we can design and produce every single specification for every customer`s different requirement.
Please check the sheet for your reference
Grade | Br | HcB | Hcj | (BH)max | Br | Hcj | Max Temp | MMPA | ||||
KGs | mT | kOe | Ka/m | kOe | Ka/m | MGOe | Kj/m³ | TK(Br)%/K | TK(Hcj)%/K | ºC | Equivalents | |
ISOTROPIC CAST ALNICO | ||||||||||||
LN10 | 6.5 | 650 | 0.48 | 38 | 0.5 | 40 | 1.25 | 10 | -0.035 | -0.025 | 450 | ALNICO3 |
LNG12 | 7.5 | 750 | 0.56 | 45 | 0.58 | 46 | 1.5 | 12 | -0.03 | -0.02 | 450 | ALNICO2 |
LNGT18 | 5.5 | 550 | 1.13 | 90 | 1.21 | 97 | 2.25 | 18 | -0.025 | 0.01 | 550 | ALNICO8 |
ANISOTROPIC CAST ALNICO | ||||||||||||
LNG34 | 11 | 1100 | 0.63 | 50 | 0.65 | 52 | 4.25 | 34 | -0.02 | 0.01 | 525 | ALNICO5 |
LNG37 | 11.8 | 1180 | 0.61 | 49 | 0.64 | 51 | 4.63 | 37 | -0.02 | 0.01 | 525 | |
LNG40 | 12 | 1200 | 0.63 | 50 | 0.65 | 52 | 5 | 40 | -0.02 | 0.01 | 525 | |
LNG44 | 12.5 | 1250 | 0.65 | 52 | 0.68 | 54 | 5.5 | 44 | -0.02 | 0.01 | 525 | |
LNGT34 | 11.5 | 1150 | 0.73 | 58 | 0.75 | 60 | 3.5 | 28 | -0.02 | 0.03 | 525 | ALNICO6 |
LNG52 | 13 | 1300 | 0.7 | 56 | 0.73 | 58 | 6.5 | 52 | -0.02 | 0.03 | 525 | ALNICO5DG |
LNG60 | 13.5 | 1350 | 0.73 | 58 | 0.75 | 60 | 7.5 | 60 | -0.02 | 0.03 | 525 | ALNICO5-7 |
LNGT38 | 8 | 800 | 1.38 | 110 | 1.4 | 112 | 4.75 | 38 | -0.025 | 0.01 | 550 | ALNICO8 |
LNGT40 | 8.5 | 850 | 1.44 | 115 | 1.46 | 117 | 5 | 40 | -0.025 | 0.01 | 550 | |
LNGT44 | 9 | 900 | 1.44 | 115 | 1.46 | 117 | 5.5 | 44 | -0.025 | 0.01 | 550 | |
LNGT36J | 7.2 | 720 | 1.88 | 150 | 1.9 | 152 | 4.5 | 36 | -0.025 | 0.01 | 550 | ALNICO8HC |
LNGT60 | 10 | 1000 | 1.38 | 110 | 1.4 | 112 | 7.5 | 60 | -0.025 | 0.01 | 550 | ALNICO9 |
LNGT72 | 10.5 | 1050 | 1.44 | 115 | 1.46 | 117 | 9 | 72 | -0.025 | 0.01 | 550 | |
LNGT80 | 10.8 | 1080 | 1.5 | 120 | 1.53 | 122 | 10 | 80 | -0.025 | 0.01 | 550 | |
ISOTROPIC SINTERED ALNICO | ||||||||||||
FLNG10 | 6.5 | 650 | 0.5 | 40 | 0.53 | 42 | 1.25 | 10 | -0.03 | -0.02 | 450 | ALNICO3 |
FLNG12 | 7.5 | 750 | 0.56 | 45 | 0.58 | 46 | 1.5 | 12 | -0.035 | -0.025 | 450 | ALNICO2 |
FLNGT18 | 6 | 600 | 1.19 | 95 | 1.23 | 98 | 2.25 | 18 | -0.025 | 0.01 | 550 | ALNICO8 |
FLNGT20 | 6.2 | 620 | 1.25 | 100 | 1.31 | 105 | 2.5 | 20 | -0.025 | 0.01 | 550 | |
ANISOTROPIC SINTERED ALNICO | ||||||||||||
FLNG34 | 11.5 | 1150 | 0.6 | 48 | 0.63 | 50 | 4.25 | 34 | -0.02 | 0.01 | 525 | ALNICO5 |
FLNGT28 | 11 | 1100 | 0.73 | 58 | 0.75 | 60 | 3.5 | 28 | -0.02 | 0.03 | 525 | ALNICO6 |
FLNGT36J | 7.2 | 720 | 1.88 | 150 | 1.9 | 152 | 4.5 | 36 | -0.025 | 0.01 | 550 | ALNICO8HC |
FLNGT38 | 8 | 800 | 1.38 | 110 | 1.4 | 112 | 4.75 | 38 | -0.025 | 0.01 | 550 | ALNICO8 |
FLNGT44 | 8.5 | 850 | 1.5 | 120 | 1.53 | 122 | 5.5 | 44 | -0.025 | 0.01 | 550 | |
FLNGT48 | 9.2 | 920 | 1.56 | 125 | 1.59 | 127 | 6 | 48 | -0.025 | 0.01 | 550 | |
BONDED ALNICO (BEARING) | ||||||||||||
B-LNG7 | 3.1 | 310 | 1 | 79.63 | 1.3 | 103.5 | 0.85 | 6.77 | -0.02 | 0.01 | 200 | |
B-LNG8 | 3.4 | 340 | 1.05 | 83.612 | 1.35 | 107.5 | 1 | 7.96 | -0.02 | 0.01 | 200 | |
Above-mentioned data are given at room temperature 20 ºC and have relationship to products` dimensions |
Neodymium Magnet,Sintered Alnico Magnet,Sintered Alnico Permanent Magnets,Sintered Alnico Ring Magnet
Honesun Industrial Co.,Limited , https://www.chinamagnetise.com