(1) The reasons for the failure of the tool to break the knife may be:
(1) The tool holder does not tighten the knife. The reason may be that the clamping claw spring pressure is too small; or the nut behind the spring is loose; or the tool is overweight; or the robotic locking lock does not work.
(2) The tool can not be loosened after clamping. The reason may be that the spring of the loose lock is too tight, and the claw cannot be retracted: the nut should be loosened so that the maximum load does not exceed the rated value.
(3) When the tool is exchanged, the tool is lost. When the tool change is changed, the spindle box does not return to the tool change point or the tool change point is drifted. When the robot grabs the tool and is not in place, the tool is started to be pulled, which will cause the knife to be lost when the tool is changed. At this time, the headstock should be moved back to the position of the tool change point and the tool change point should be reset.
(2) The robot fails to extend the tool to pull out the tool from the spindle and the tool magazine. The cause of the failure may be:
(1) "loose knife" sensor switch failure In the process of tool change, the completion signal of each action is sent by the sensor switch, and the next action can only be performed after the previous action is completed. The third step is “spindle loosening knifeâ€. If the sensor switch does not signal, the robot “pull the knife†will not move. Check the two sensor switches and the signal is normal.
(2) The "loose knife" solenoid valve fails. The "loose knife" of the main shaft is completed by the solenoid valve turning on the hydraulic cylinder. If the solenoid valve fails, the hydraulic cylinder will not enter the oil and the tool will be “looseâ€. Check that the spindle's "loose knife" solenoid valve is operating normally.
Common fault analysis of robots
(3) “Loose knife†hydraulic cylinder does not operate due to insufficient pressure or oil leakage in the hydraulic system, or the stroke is not in place to check the cutter cylinder hydraulic cylinder, the action is normal, the stroke is in place; open the headstock (Fig. 8-2) rear cover Check the spindle loose-knife hydraulic cylinder and find that it has reached the position of the loose knife, the oil pressure is also normal, and the hydraulic cylinder has no oil leakage.
(4) There is a problem with the manipulator system, and the condition of “pull the knife†cannot be established. The reason may be that there is a problem with the motor control circuit. Check that the motor control circuitry is normal.
(5) There is a problem with the spindle system. The schematic diagram of the spindle structure is shown in Figure 8-2. The cutter pulls the pull end of the tool shank by the disc spring through the pull rod and the spring chuck; when the knife is loosened, the piston rod of the hydraulic cylinder presses the ejector rod, and the ejector rod pushes the pull rod through the hollow screw, and on the other hand, the spring chuck Loosen the pull stud of the tool and push the pull stud on the other hand to make the tool move to the right and become "loose" in the taper hole of the main shaft.
(3) The reason why the spindle system is not loosened is estimated to have the following four points:
(1) The length of the tool pull pin is not enough, so that the hydraulic cylinder has been moved in place, but the tool top has not been loosened;
(2) The position of the hollow screw at the end of the tie rod has changed, so that the stroke of the hydraulic cylinder can not meet the requirements of the "loose knife";
(3) The ejector has a problem, which has been deformed or worn;
(4) The spring chuck is faulty and cannot be opened;
(5) When the spindle assembly is adjusted, the tool movement amount is adjusted too small, so that some comprehensive factors in the use process can not meet the "loose knife" condition.
Approach:
Remove the "loose knife" hydraulic cylinder and check that the fault is the adjustment of the "extension" of the cannulated screw when the assembly is assembled. Therefore, the "loose knife" hydraulic cylinder stroke is in place and the tool is in the spindle taper hole. "Extrusion" is not enough and the tool cannot be removed. Adjust the "extension amount" of the cannulated screw to ensure that the amount of extrusion of the shank in the spindle taper hole is 0.4~0.5mm after the stroke of the spindle "loose knife" hydraulic cylinder is in place. After the above adjustment, the fault is eliminated.
Conclusion
With the increase of cutting speed and the shortening of cutting time, the requirements for tool change time are gradually increasing. The speed of tool change has become an important indicator of high-level machining centers.
Since the automatic tool change of the machining center is reliable and accurate, and the structure is relatively complicated, it is technically difficult to increase the tool change speed. At present, high-speed machining centers produced by foreign advanced machine tool enterprises are equipped with fast automatic tool changers in order to adapt to high-speed machining. Many adopt new technologies and new methods.
The technical level of functional components, the pros and cons of performance and the overall level of social support directly determine and influence the technical level and performance of CNC machine tools, and also limit the development speed of the mainframe. The tool changer is a key function for the stable and reliable operation of the machining center. Its fast and accurate tool change program is an important factor affecting the efficient and reliable processing performance of the machining center. Without a tool changer, it is impossible to have a machining center with a centralized process. According to the data, the failure rate of the tool magazine and robot accounts for about 25% of the failure rate of the whole machine [1]. Therefore, the performance and quality of the tool changer directly affects the performance, quality and variety of CNC machine tools.
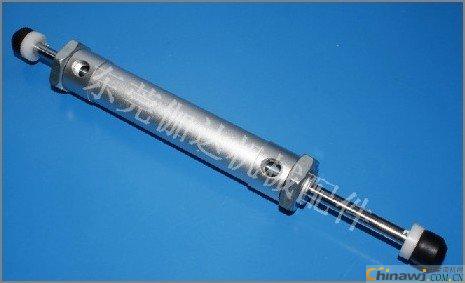
InVent PS – a series of Monodisperse Reversed Phased Polymeric Resin designed for the polishing purification and separation for pharmaceuticals and natural products. These resins are made of polystyrene, with the advantages of high resolution and loading capacity and long shelf-life. It also shows an excellent stability in organic solvent, strong acid and base system, as well as a good tolerance to high salinity, without any tailed peak caused during the separation for alkali compounds.
By the benefits of its good performance and superior chemical and pH stability, InVent PS is widely used in the purification for pharmaceuticals, modern Chinese traditional medicine, natural health care products, high-class drink and so on.
Reversed Phase Polymeric Resin
Reversed Phase Polymeric Resin,Monodisperse Polymeric Monodisperse Resin,Polymeric Resin,Reverse Phase Polymer Resin
Nanjing Genshine Bio-technology Co., Ltd , http://www.genshine-bio.com